
Processes
we all use them
Every day we perform both routine and adhoc activities in business. These are processes. The visualisation of workflows through mapping provides immense opportunity for efficiency and effectiveness improvements.
hard to see the woods for the trees
Workflow mapping shows how performance is dependent on resources and processes working together. It is possible to see the machines and people operating, but it can be difficult to visualise the workflow without a pictorial view of the workflow map. Once this picture is created, it can be improved, controlled and ultimately managed.
is there a better way
Inefficient processes can be frustrating and difficult to change or improve. Each person involved in a workflow can have their own way of working, but workflow mapping is a tool that opens up the processes for others to visualise and improve them.
Process Improvement
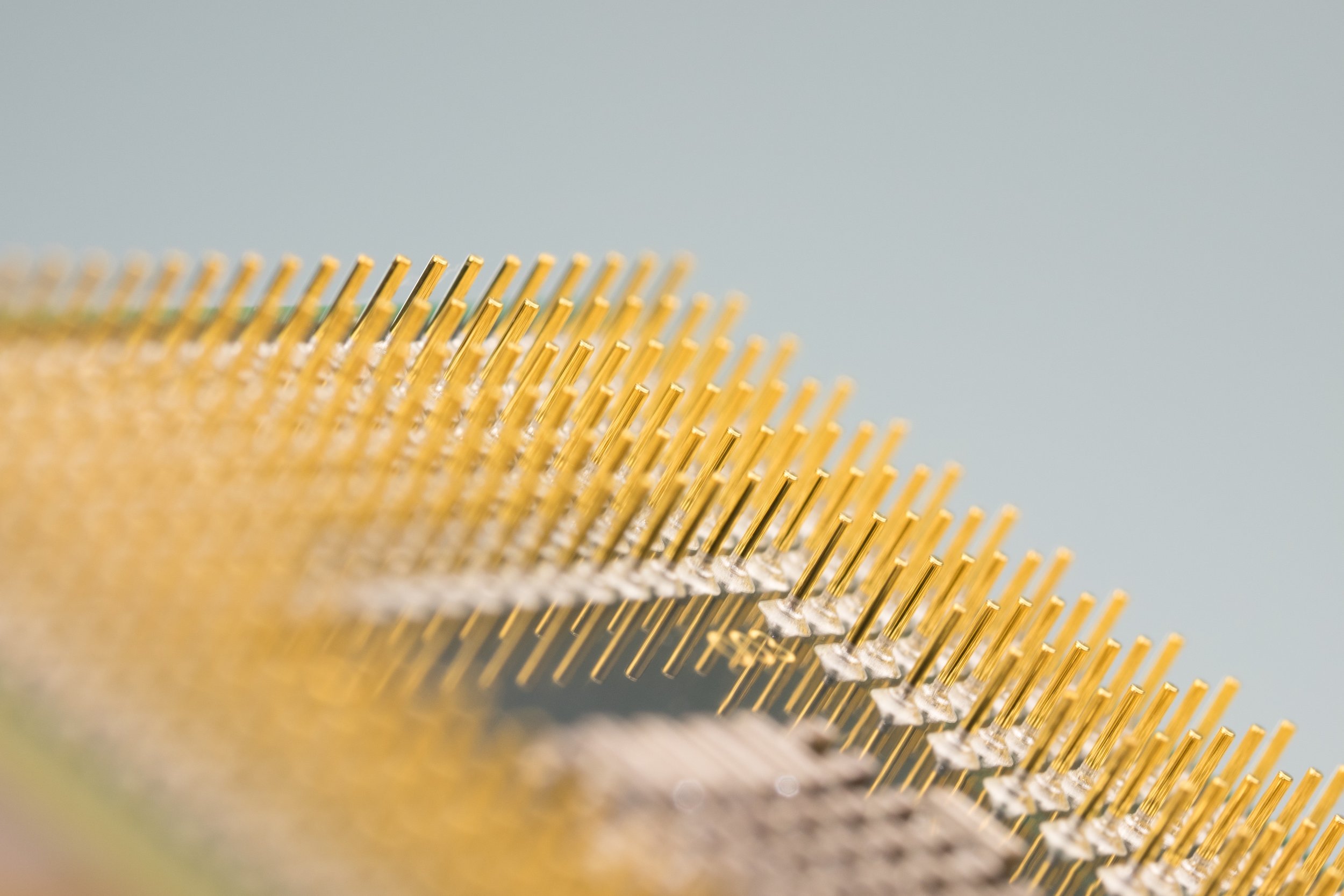
Building a quality Brand
Tools & methodologies
Building a quality brand relies on a culture of continuous improvement and this culture must come from organisational leaders. Change is inevitable and companies must adapt and improve to remain competitive. While there are dozens of methodologies for process improvement available (PDCA, Lean, Six Sigma, 5S, TQM to name a few), our approach is to simply identify where we can save you time, money, energy and stress.
Consistency Measures
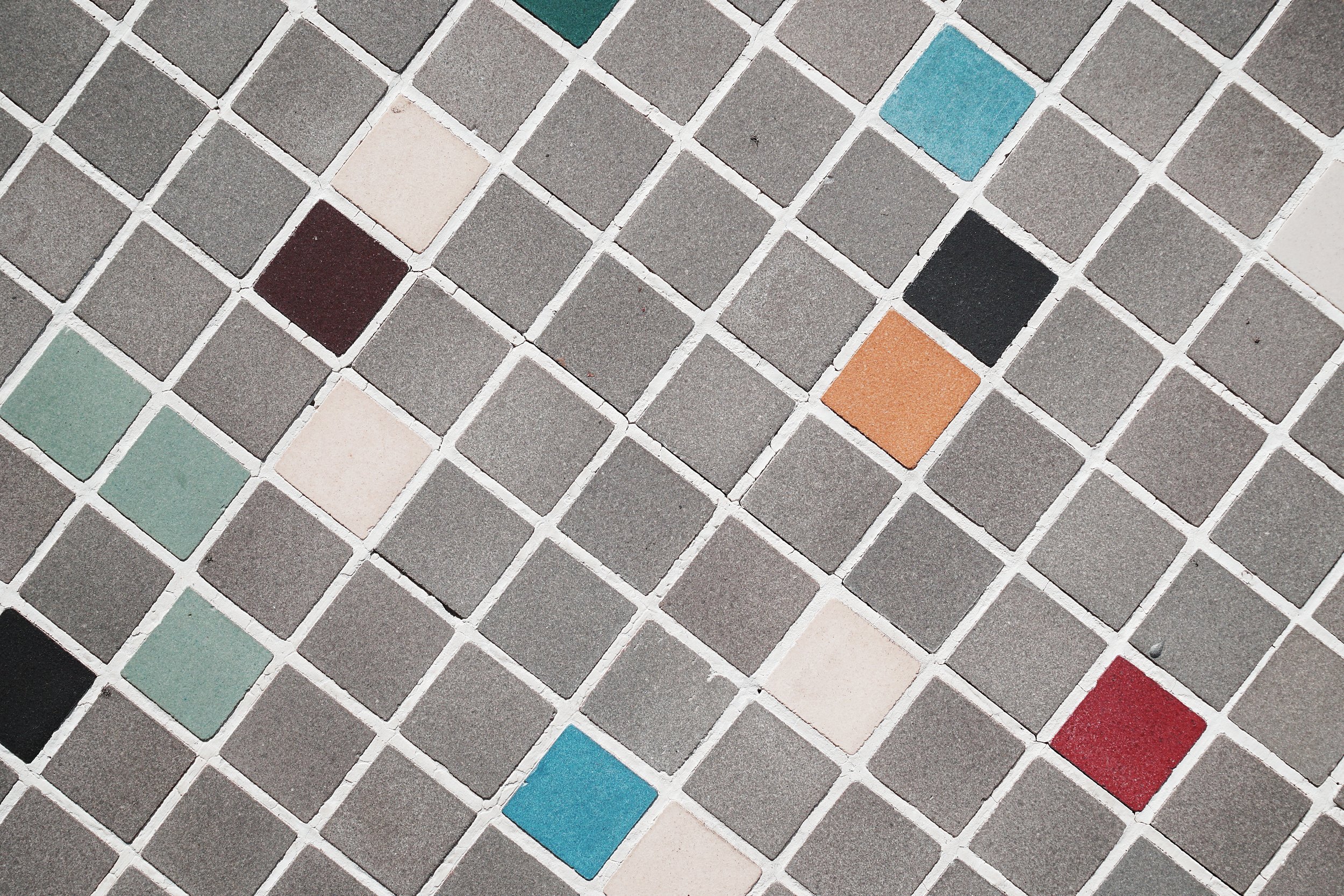
Knowing where to start
key performance indicators
Measurement is the key to understanding how successful (or not) your process improvement efforts have been. The first step is taking a baseline measurement, implementing a change and remeasuring to assess the impact of that change. If the impact is positive, the improvement is implemented on a wider scale. If not, we try a different improvement.